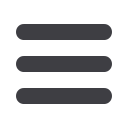

Analyze 40% More Samples per Shift
Using Split Injection for Semivolatiles
By Michelle Misselwitz, Innovations Chemist, and Jack Cochran, Director of New Business and Technology
Semivolatiles are typically analyzed using splitless injection, but this
approach results in slow analysis times and injection-to-injection vari-
ability. Combined, these factors reduce the number of samples that
can be analyzed before quality control criteria are no longer met. This
article demonstrates the advantages of split injection in terms of sam-
ple throughput, sensitivity, and linearity for EPA Method 8270D.
Increase Sample Throughput with Faster Oven Cycles
Split injection produces narrower injection bands and uses higher ini-
tial oven temperatures than splitless injection. Two oven programs
starting at 80 °C were compared to a typical splitless program, and the
faster oven cycle times used with split injection allowed up to 10 more
samples to be analyzed per shift (Table I). The fastest program resulted
in reduced separation of dibenz(a,h)anthracene and indeno(1,2,3-
cd)pyrene (Figure 1), but these compounds were fully resolved using
the alternate split conditions. The 80 °C oven start temperature could
not be used with splitless injection, as it resulted in extremely broad
peaks that could not be integrated.
Split Injection Results in More Reliable Sensitivity
and Excellent Linearity
In addition to increasing sample throughput, split injection provided
good sensitivity and better injection-to-injection repeatability at
0.5 ng on-column than splitless injection. Minimum response factor
criteria were easily met and lower relative standard deviations
(% RSD) for base/neutral and acid extractable compounds were
achieved at the lowest calibration level (Table II). Calibration curves
(5-160 ng/μL) were also assessed and, even with the 10:1 split,
response factors met the method criterion of <20% RSD, except for
2,4-dinitrophenol (Table III). In this case, calibration was established
based on the correlation (r = 0.9997). Better repeatability at low lev-
els makes it easier to meet method criteria and allows more injec-
tions to be made before maintenance is required.
• Faster oven cycle increases sample throughput.
• Better precision at trace levels, compared to splitless
injection.
• Reliably meet or exceed method requirements for
sensitivity and linearity.
Split (Fast Cycle)
Split (Faster Cycle)
Splitless
Total run time (min.)
21
18.5
25.5
Sample analysis (min.)
18
15
20
Oven cooling (min.)
3
3.5
5.5
Sample throughput*
(Samples/shift)
30
34
24
% Increase in sample
throughput (vs. splitless)
25%
42%
--
* 12-hr. shift = 10.5 hr. sample analysis period + 1.5 hr. quality control/method
performance analysis period. Sample throughput calculation based on number of
samples that can be analyzed in 10.5 hours.
Table I
Split injection significantly increases sample throughput
compared to splitless injection.
Table II
Using split injection results in greater repeatability at
0.5 ng on-column, allowing more samples to be analyzed
before maintenance is required.
Split (10:1)
Splitless
8270D Min. RF RF %RSD
RF %RSD
Pyridine
--
1.534
2
1.038
9
Phenol
0.800
1.861 0.7
1.857
5
1,4-Dichlorobenzene-d4
ISTD ISTD ISTD ISTD ISTD
N-Nitroso-di-
n
-propylamine 0.500
1.053
2
1.266
3
2,4-Dichlorophenol
0.200
0.317
2
0.325
3
Naphthalene-d8
ISTD ISTD ISTD ISTD ISTD
Naphthalene
0.700
1.249 0.5
1.238
2
Hexachlorocyclopentadiene 0.050
0.407
1
0.414
5
2-Nitroaniline
0.010
0.395
3
0.514
3
Acenaphthylene
0.900
2.188 0.9
2.139
1
Acenaphthene-d10
ISTD ISTD ISTD ISTD ISTD
2,4-Dinitrophenol
0.010
0.113
8
0.127 13
4-Nitrophenol
0.010
0.256
6
0.296
5
4,6-Dinitro-2-methylphenol
0.010
0.175
6
0.110
9
N-Nitrosodiphenylamine 0.010
0.712
1
0.694
1
Pentachlorophenol
0.050
0.115
3
0.098
5
Phenanthrene-d10
ISTD ISTD ISTD ISTD ISTD
Phenanthrene
0.700
1.252 0.7
1.259
2
Perylene-d12
ISTD ISTD ISTD ISTD ISTD
Benzo(ghi)perylene
0.500
0.940
4
0.252 26
Avg. %RSD 3 Avg. %RSD 6
Comparison based on faster cycle split conditions shown in Figure 1; 0.5 ng
on-column (n = 5).
ISTD = internal standard
Environmental
8
www.restek.comWebsite :
www.chromtech.net.auE-mail :
info@chromtech.net.auTelNo : 03 9762 2034 . . . in AUSTRALIA