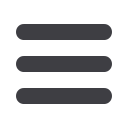

•
14
•
2007 vol. 4
Restek Performance Coatings
Sulfinert® Treated Systems Preserve
ppb Levels of Active Sulfur Compounds
By Gary Barone, Martin Higgins, David Smith (Restek Performance Coatings Division);
Shawn Rowan and Warren J. Gross (O’Brien Corporation); and Phil Harris (Harritec LLC.)
• Sulfinert® treatment prevents adsorption of sulfur compounds, ensuring representative sampling.
• Improved accuracy allows precise control of downstream processes, for better efficiency and profitability.
• Shorter cycles translate directly into increased sample throughput.
Many volatile sulfur compounds adsorb strongly to metal surfaces in sampling, storage, and transfer apparatuses. In addition to caus-
ing inaccurate values, adsorption can prolong analysis cycle times. To compare quantitative losses of active sulfur species, we sam-
pled, stored, and transferred low ppmv to low ppbv concentrations of active sulfur gases, using control (untreated) and Sulfinert®
treated system components.
Preventing Sulfur Compound Losses During Storage
Figure 1a depicts results from a comparison in which a gas containing 17ppbv of hydrogen sulfide was stored for 7 days in untreated
or in Sulfinert® treated stainless steel sample cylinders. The response ratio for hydrogen sulfide, relative to a stable reference material,
dimethyl sulfide, is steady at approximately 1:1 for at least 7 days in Sulfinert® treated cylinders. The data show a Sulfinert® treated
system will reliably store ppb levels of the active sulfur-containing compound during transport from the sampling site to the ana-
lytical laboratory. In contrast, hydrogen sulfide degraded rapidly in the untreated cylinder, and was lost totally within 24 hours. In a
similar study in which gas containing 18.8ppbv methyl mercaptan was stored for 60 hours in Sulfinert® treated sample cylinders,
recovery of the active sulfur compound was equally high relative to the stable reference material, dimethyl sulfide, as shown in Figure 1b.
Sample Transfer: Adsorption of Sulfur Compounds to Tubing
Comparison of Sulfinert® treated electropolished stainless steel tubing (TrueTube® EPS tubing, O’Brien Corporation, St. Louis,
MO), untreated electropolished stainless steel tubing (TrueTube® EP tubing, O’Brien Corporation), and raw commercial grade 316L
stainless steel tubing showed Sulfinert® treated electropolished tubing has the inertness necessary for quantitatively transferring low
ppmv to low ppbv concentrations of sulfur compounds.
To determine whether an active sulfur-containing compound in a gas stream would adsorb to active sites on the transfer tubing
surface, we monitored the length of time that elapsed before recovery values for a sulfur compound exiting a 100-foot (30.5-meter)
length of tubing were stable and accurate, using helium containing 0.500ppmv methyl mercaptan as the test material, at a flow rate
of 40cc/minute. Figure 2 shows Sulfinert® treated electropolished tubing did not adsorb methyl mercaptan to any measurable extent,
delivering a representative sample with no delay. When adsorption of sulfur-containing compounds is prolonged, desorption from
the surface also is slow. This “memory” of adsorbed compounds can cause long delays in re-equilibrating a sample pathway. In Figure 3,
Sulfinert® treated tubing shows the lowest retention of sulfur compounds, by several orders of magnitude. Samples can be evaluat-
ed,with accurate results and with no delay between them.
Figure 1
Sulfur compounds are stable in Sulfinert® treated cylinders, assuring a representative sample is delivered.
a) 17ppbv hydrogen sulfide in 500mL cylinders
b) 18.8ppbv methyl mercaptan in 300mL cylinders
The authors thank Shell Research and Technology Centre, Amsterdam, for the data used in evaluating sulfur gas uptake and the memory effects of tubing substrates.